Pour les fabricants de tuyaux ou de profilés de moyenne ou grande taille, le mélange, le transport et l'alimentation artificiels traditionnels ne peuvent pas répondre aux besoins de la production automatique actuelle. L'ensemble complet d'installations chimiques automatiques adaptées aux besoins des clients par Liansu Machinery comprend le stockage des matières premières, la livraison des matériaux, le pesage et le mélange, et la livraison automatique du mélange à la production de l'extrudeuse.
Liansu Machinery s'est engagée à construire un système de mélange et d'alimentation automatique à commande centrale pour réduire les coûts de main-d'œuvre, améliorer la qualité des produits, améliorer l'efficacité de la gestion de la production et fournir un meilleur environnement de travail.
Case One
Premier cas
L'atelier d'un client construit tôt, la salle de mélange et la chaîne d'extrusion se trouvent à deux endroits différents, la chaîne de production a besoin de travailleurs pour transporter le matériel dans une voiture de la salle de mélange à la zone de matériel de la chaîne de production. La distance entre deux endroits est d'environ 150m.
Après la transformation, l'atelier a réduit de 5 employés, si le salaire mensuel est de 5 000 RMB, le coût que nous économisons en un an est de 300 000 RMB, l'environnement de l'atelier est meilleur après la transformation, la stabilité du personnel est plus élevée.

Programme d'alimentation des ateliers
À l'heure actuelle, l'atelier compte au total 16 lignes de production, 9 machines de mélange et 1 formulation. Après un examen approfondi, nous décidons que chaque 2 machines de mélange transportent la phase dense et l'envoient au silo intermédiaire de la ligne de production. Chaque silo intermédiaire correspond à 1 chaîne de tuyaux, 4 lignes d'extrusion, et le reste de la machine de mélange est de réserve, le mélange peut être envoyé à chaque machine.
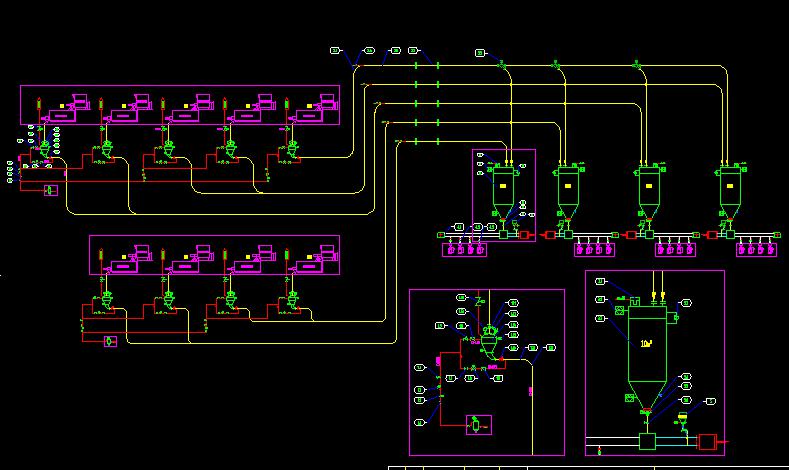
Après la transformation de l'atelier
L'alimentation de la machine de mélange, les allers-retours artificiellement transportent le matériau à la machine, ce mode prend du temps et est laborieux, l'environnement de travail est trop mauvais pour satisfaire la norme de production de protection de l'environnement moderne.
Après la transformation de l'atelier
Conduite de transport de matériaux à l'extérieur de l'atelier.
La zone d'alimentation de la chaîne de production est désormais alimentée automatiquement par le convoyeur à chaîne de chaque chaîne de production, sans alimentation manuelle. Après la transformation, on obtient un transport sans poussière, qui répond aux besoins de la production et offre un environnement de production sain.
Case Two
Deuxième cas
L'atelier de PVC du client B a été construit d'après la conception originale de l'usine de quatrième génération. La partie centrale de l'atelier est la zone de mélange des matériaux, qui comprend au total 4 couches, la quatrième couche comme zone de stockage des matières premières, la troisième couche comme zone de pesage des matières premières, la deuxième couche comme machine de mélange et la première couche comme zone de production de la ligne d'extrusion. La zone d'alimentation en matières premières se trouve dans un autre atelier au premier étage, et les matériaux sont transportés par transport pneumatique vers la zone de stockage des matières premières du quatrième étage.
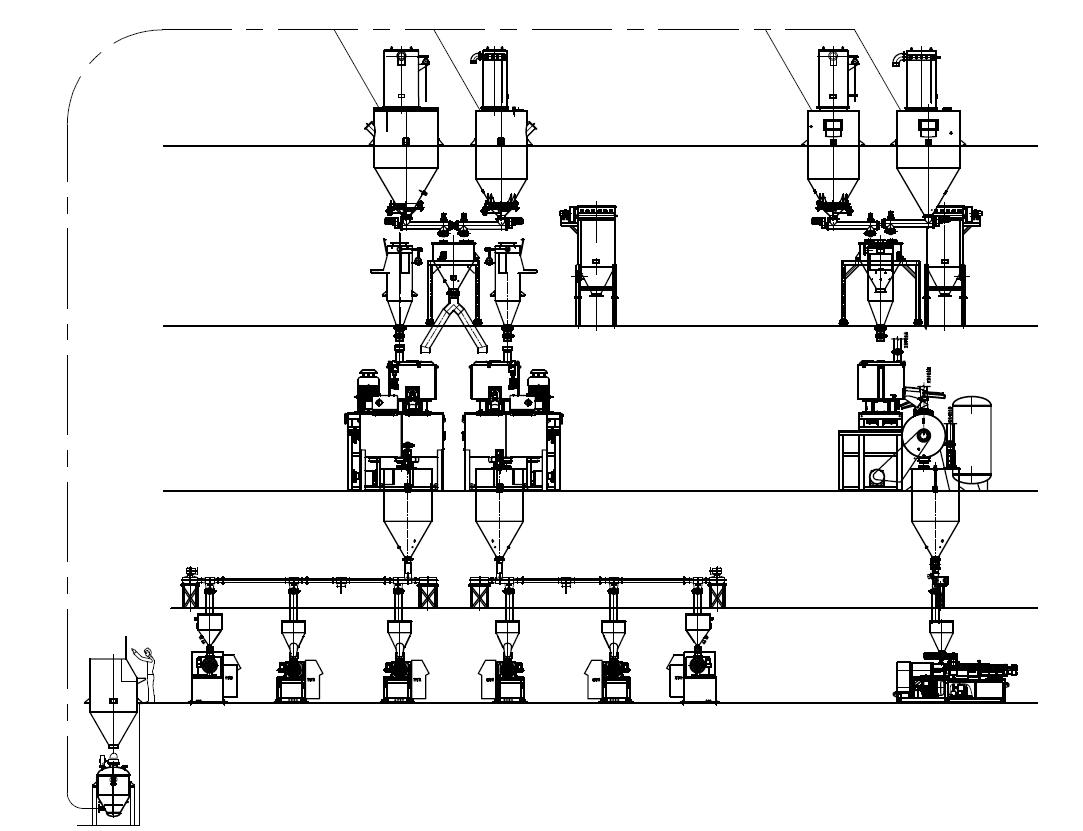
Programme d'alimentation des ateliers
Une zone d'alimentation centralisée est propice à une gestion efficace des matières premières.
Au-dessus de la station d'alimentation, un trou d'alimentation de sacs de tonne peut être installé, la station simple et double peut être sélectionnée pour la station d'alimentation. Pour la station d'alimentation à double station, deux personnes s'alimentent en même temps pour réduire l'intensité de travail lorsque la tâche de production est lourde.
Le silo de stockage est utilisé pour le stockage du matériau principal, le PVC et le CaCO3, et la soupape de décharge est installée au-dessus du silo. Lorsque la pression du silo atteint la valeur de consigne, la soupape relâche automatiquement la pression et joue le rôle de protection de sécurité.

Chaque type de matériau passe par la trémie de stockage, et en dessous se trouve l'alimentateur à vis. L'alimentateur à vis est contrôlé par l'ordinateur. Le matériau est acheminé vers la balance électronique, pour peser chaque type de matériau à tour de rôle.
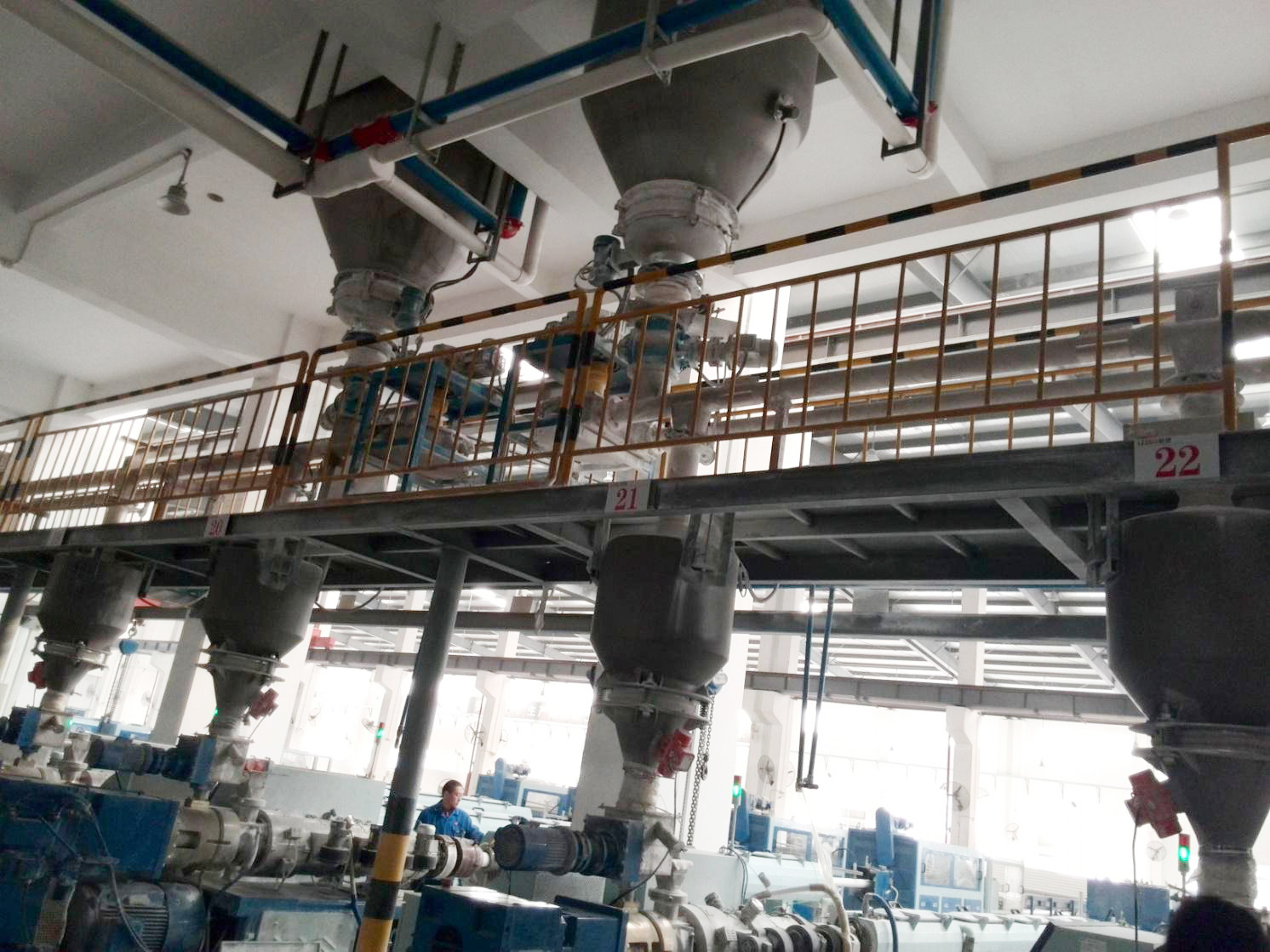
Grâce au convoyeur à chaîne, chaque matériau est automatiquement acheminé vers la chaîne d'extrusion, et l'opération de travail manuel dans le processus intermédiaire est supprimée.
Case Three
Troisième cas
L'atelier de PVC du client alimente automatiquement le PVC et le CaCO3, par alimentation manuelle, livraison continue à basse pression, stockés dans cinq grands silos de 100 m3, et le matériau est livré à la machine de mélange par pesage à pression négative, puis le mélange est transporté vers la machine pour être utilisé par la pompe du silo. Le système utilise un grand silo pour stocker les matières premières, et le matériau dans le silo peut répondre aux 8 heures d'utilisation de la machine. De cette façon, le matériau peut être alimenté par l'équipe de nuit lorsque le coût de l'électricité est au plus bas pour une utilisation de jour.
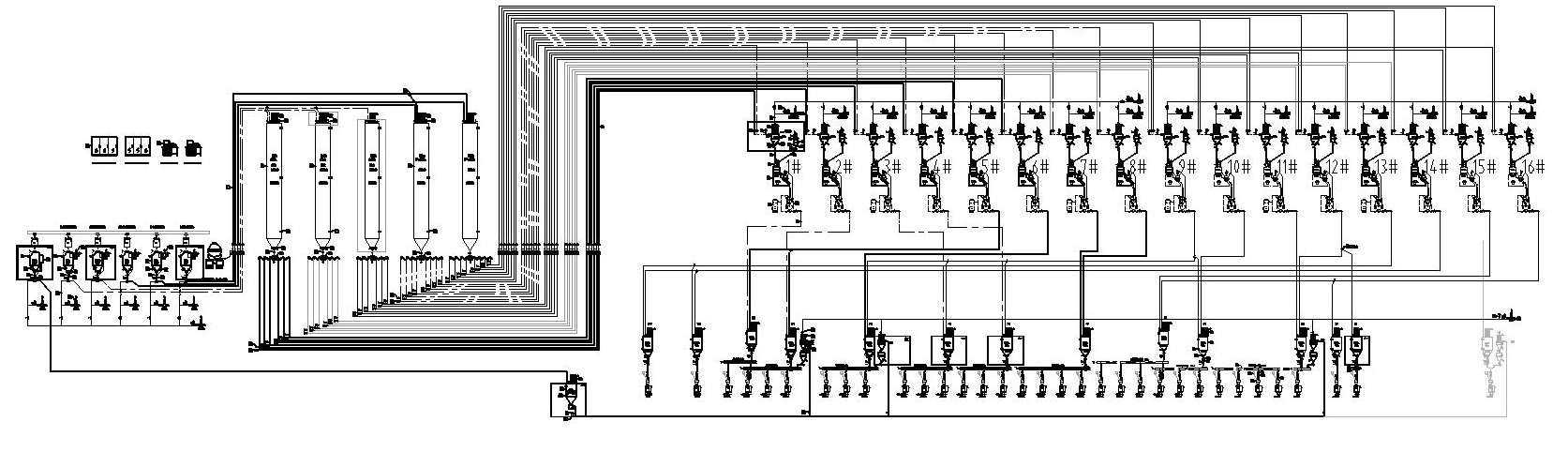
Programme d'alimentation des ateliers
Atelier d'alimentation manuelle
Transport de matériaux à basse pression
Silo de stockage extérieur de 100m3 de PVC et CaCO3, dont le fond est la boîte de distribution de l'aspiration à pression négative.
Atelier de pesage des matières principales et d'alimentation des formulations
Atelier de mélange, utilise une pompe à silo pour transporter le mélange